Contents and quick links:
What is Smoke Ventilation?
What are the legal requirements for smoke ventilation systems?
What does a smoke ventilation system look like?
How do smoke ventilation systems integrate with fire alarms and other building systems?
What is the difference between natural and mechanical smoke ventilation?
What are the main components of a Smoke Ventilation System?
System schematics for a typical smoke ventilation system
What is primary zone lockout for a smoke ventilation system?
Mechanical v Natural Smoke Ventilation
What is Natural Smoke Ventilation?
What is Mechanical Smoke Ventilation?
Choosing the right smoke ventilation system
What are the regulations for smoke ventilation?
Introduction to smoke vent standards and regulations
The UK Regulatory Framework
Smoke Ventilation and The UK Building Regulations
What is approved document B?
Regulations, standards and guidance during the design stages
Approved Document B
Smoke control of common escape routes by natural smoke ventilation
Smoke control of common escape routes by mechanical ventilation
What is the required free area of a smoke vent or automated opening vent (AOV)?
How do you calculate the free area of a smoke vent or AOV?
Other Guidance and Standards
The British Standards
BS7346-8: Code of Practice for planning, design, installation, commissioning and maintenance of smoke control systems
BS9991:2015 Fire safety in the design, management and use of residential buildings. Code of practice
What are the recent changes to BS9991 in 2024 for smoke ventilation?
BS9999: Code of practice for fire safety in the design, management and use of buildings
BS7974: Application of fire safety engineering principles to the design of buildings
What are the product standards for components of Smoke Ventilation Systems?
The Construction Product Regulations and Product standards
BS EN12101 and CE / UKCA Marking
Fire Safety Laws and Regulations
Fire Safety Act 2021
Fire Safety (England) Regulations 2022
Installation of smoke ventilation systems and components
Commissioning, Testing and sign off
Testing and Maintenance of Smoke Ventilation Systems
How often should a smoke ventilation system be tested?
What is a competent person for maintaining smoke ventilation systems?
What about replacement parts and actuators to AOVs?
Documentation and the Golden Thread
What is the Golden Thread?
Evolving standards and guidance
About Teal Products
What is Smoke Ventilation?
Smoke Ventilation systems play a critical role for the safety of building occupants in larger and multi storey buildings, where they are called upon in the event of a fire to keep escape routes clear of smoke and help occupants to safely exit the building.
Smoke vent systems are commonly employed in high rise residential, commercial, education, hotel and industrial buildings, and are subject to a variety of standards and regulations to ensure that the smoke ventilation strategies and components that deliver them have been properly selected, fitted and maintained so that they can be depended upon in the event of a fire.
What are the legal requirements for smoke ventilation systems?
Because smoke vent systems are depended upon for life safety in the event of a fire, they are subject to a suite of legislation, building regulations and product standards imposing legal requirements for the various parties involved with the design, manufacture, installation, and maintenance of buildings.
The various documents offer guidance, help clarify responsibilities, and outline the means of fulfilling them – ultimately to ensure the ongoing safety of occupants throughout the life of the building.
All parties involved with the design and specification, purchasing, installation, management, and ownership of buildings should ensure they are familiar with the latest standards and regulations to be confident in their compliance in order to fulfil their legal duties and keep occupants safe. We go into more detail on the regulations and standards for smoke ventilation in our article here.
What does a smoke ventilation system look like?
Smoke ventilation systems consist of a series of components often including smoke sensors, AOV windows, roof vents, louvres and fans which are carefully located and operated by a control panel to clear exit routes of smoke in the event of a fire.
If you’ve ever been in a large building as a member of the public or resident, and noticed orange break glass units on walls, louvred panels in corridors, automatic operators connected to roof windows, or large fan units on the roof of buildings – you’ve probably seen some of the common components of Smoke Ventilation Systems. These are most obvious in multi storey buildings with longer corridors, atriums, and staircases. Experts in smoke ventilation will also recognise the many other elements that are less obvious – and we’ll take a look at those in more detail in this section.
The actual solution employed, and components that make up the smoke ventilation system, will have been selected by the building Architects and Engineers during its design. Older buildings will often have had their systems or components upgraded during their life and routine maintenance, to bring them into alignment with current standards and guidance.
Designers will have referred to best practices, design standards and regulations to determine the most appropriate solution according to the type of building, users, and challenges that may exist in the event of a fire – for example type of users, how many people may need to escape the building, and the distance and number of floors they would need to travel.
These factors will also influence many other elements of the building design like the number and location of stairwells, and whether sprinkler systems are required. In larger buildings the smoke ventilation system is commonly interlinked to the fire alarm system although they are normally treated as separate specialist systems.
There are typically two fundamental approaches to Smoke Ventilation – Natural and Mechanical Smoke Ventilation;
Both approaches use a series of components fitted in the building structure to ensure the extraction of smoke from key areas in the building – normally the common corridors and stairs that make up the main escape routes, and sometimes additional fire fighting facilities.
The system operation and component choices are designed and selected according to a smoke vent strategy to best suit the building. The way in which the system will operate is defined by a description of operation (DesOps) also known as a cause and effect, which sets out which components will operate where and when, depending on where a fire is detected.
Want help with system design or component selection? Explore products here or send us an email to sales@tealproducts.com
How do smoke ventilation systems integrate with fire alarms and other building systems?
Smoke ventilation systems may have to integrate with other building systems such as fire detection systems, fire alarms, sprinklers, emergency lighting and BMS or remote monitoring systems. They may share interoperable signals or strategies, so integration through good design practice and co-ordination between specialists delivering the different systems is crucial.
What is the difference between natural and mechanical smoke ventilation?
The main difference is that mechanical systems use fans to create pressure differences to draw or force smoke out of key areas of the building. Natural smoke ventilation systems use a series of automatic opening vents at high and low level, utilising natural buoyancy to exhaust the smoke.
In larger buildings the systems may have an element of natural and mechanical smoke ventilation, or share common components.
Approved document B of the building regulations normally assumes a Natural approach to Smoke Ventilation in buildings up to 30m tall, although mechanical smoke ventilation is also allowed providing it is properly engineered and can be demonstrated to perform at least as well as the requirements set out in ADB and BS EN12101-6.
Buildings above 30m tall require mechanical smoke ventilation solutions.
What are the main components of a Smoke Ventilation System?
The main components that often make up a smoke ventilation system are smoke detectors, smoke control panels, automatic opening vents (or AOVs), stairwell vents, smoke shafts, louvres, fans and break glasses – as well as system wiring, backup power supplies and status displays or HMI screens.
Here’s some more details about the common components that make up a smoke vent system:
- Smoke detectors – to detect smoke from a fire. These can be a part of the fire alarm system which may be interlinked to the smoke ventilation controllers to share the relevant zone fire or smoke detection status and in turn trigger the smoke ventilation system to respond accordingly.
- Break glass units – to allow users to manually activate the system or specialist fire services to test or reset it.
- Automatic or Automated Opening Vents – commonly known as AOV’s and which may be in the form of AOV windows, AOV louvres, AOV dampers, AOV doors, AOV rooflights or AOV roof vents. These are also sometimes knows as Smoke and Heat Exhaust Ventilators, or SHEVs.
- Fans – sized and specified according to the application.
- Wiring – fire performance cabling to withstand potential affects of a fire and connect all the relevant components for signals and/or power.
- Smoke control panels or AOV panels – single zone, multi zone, or interlinked – and configured to deliver the DesOps or Cause and Effect required for the system.
- HMI screens or status displays – HMI (Human Machine Interface) screens are frequently used in larger systems to display system health and status of zones across the building and system.
- Fire officer / Fireman’s override switch – these switches are protected and may form part of the break glass to allow fire officers to manually force local vents to operate open or closed as part of their firefighting strategy.
Each of the components will have been selected to serve a specific area or ‘smoke zone’ within the building and have its performance requirements determined and specified to ensure it meets the guidance and requirements of that space. For example, AOV’s in different locations must achieve certain opening areas, fans must achieve certain extraction rates or pressure capacities, and wiring must be resilient to fire conditions.
There are normally multiple factors that dictate the performance requirements of each component. They must also be selected to be compatible with one another to create a holistic system which will be effective in the event of a fire. Almost all components must be able to withstand and maintain their performance under fire operating conditions, like primary mains power failure and exposure to high temperatures, for an agreed period of time.
Collectively the system must still be able to operate if the primary power supply fails to continue to protect the building in the event of a power failure, or as a result of the fire affecting electrical supplies. Systems therefore require an acceptable secondary power supply – often via a UPS (uninterrupted power supply) for mechanical smoke ventilation using mains powered fans, or battery backup for natural smoke ventilation using extra low voltage (24v DC) components. Battery backup offers a cost-effective means of providing power to extra low voltage components in Natural Smoke Ventilation systems with batteries normally integral to the local AOV controllers / Smoke Control Panels, and subject to regular test and routine replacement.
System schematics for a typical smoke ventilation system
Many of the approaches taken by designers, and performance requirements of the individual components, will have been derived from guidance in standards like the building regulations, or by modelling and analysing the requirements according to the specific building.
Systems can therefore vary between different types and sizes of buildings, but here’s a couple of typical examples of system schematics.
Schematic of a simple single stairwell natural smoke ventilation system
Featuring a certified automatic opening rooflight or high level AOV window of 1m2 at the head of the stairs as the automatic opening vent (AOV) powered and controlled by a smoke control panel with integrated backup battery, triggered by a smoke detector, connected to a fireman’s override switch located at the building entrance, all wired in appropriate fire performance cabling (schematic also shows optional manual override switch for comfort ventilation, and rain sensor to close in the event of rain).
This type of system might be common in smaller blocks of flats with a single stairwell meeting the description of ‘small single stair buildings’ as defined in ADB;
The Building Regulations ‘Approved document B’ gives guidance on what qualifies as a small single stair building – for example smaller blocks of flats with a maximum of 3 floors above ground level – with at least one floor above 4.5m from ground level, and a maximum top floor level of 11m. The maximum travel distance must be no more than 4.5m in one direction from the flat entrance door to common stair or stair lobby, with flats being separated from the common stairs by a protected* lobby or corridor (*protected lobbies or corridors are those with sufficient fire-resistant construction to prevent fires in flats from quickly spreading to the escape route).
See below extract from Approved Document B for more information:
Schematic of a larger natural smoke ventilation system
Featuring a certified automatic opening rooflight of 1m2 at the head of the stairs as an automatic opening vent (AOV), powered and controlled by a smoke control panel with integrated battery backup. Interconnected with other control panels for control of a certified 1m2 louvred smoke damper on each floor from the corridor into a 1.5m2 sectional area smoke shaft, 1m2 AOV louvred smoke ventilator at the head of the smoke shaft, and certified 1.5m2 AOV smoke louvres or AOV windows situated as high as possible on an external wall at the end of corridors.
Smoke / fire zones are monitored by smoke detectors, connected to an orange smoke vent break glass unit and all wired in fire performance cabling to the smoke control panels. The smoke control panels are networked and arranged in a master slave configuration, configured to only open the head of stair, smoke shaft vent, and the appropriate smoke shaft damper and corridor vent on the floor where the fire is first detected to achieve primary zone lockout.
This type of system might be common in larger blocks of flats and hotels.
Approved Document B offers guidance on buildings like this that don’t qualify as small single stair buildings:
What is primary zone lockout for a smoke ventilation system?
Primary zone lockout for smoke ventilation systems was established in ADB 2019 & subsequently BS9991:2024 stating that vents from corridors or lobbies on floors other than where the fire is first detected should be closed & remain closed even if the fire is later detected on other floors to help prevent fire crossover
Mechanical v Natural Smoke Ventilation – Which is best, Natural or Mechanical Smoke Ventilation?
The approach used must be fit for the purpose and building to which it is being applied. Natural ventilation may be considered cheaper, easier to integrate into the building and lower cost, whereas mechanical smoke ventilation can take up less space in larger buildings.
Although there are two fundamental approaches, the one chosen must follow the regulations and meet the requirements for the building.
What is Natural Smoke Ventilation?
Natural smoke ventilation uses carefully specified vents around a building to systematically operate in the event of a fire. The vents, often located in stairwells, lobbies, corridors or smoke shafts, are normally operated automatically in a particular combination to utilise the natural buoyancy of warm air to clear smoke.
Natural Smoke Ventilation utilises carefully considered vent locations and sizes, in conjunction with the natural buoyancy of hot smoke, to encourage smoke to be exhausted through high level vents, often known as Automatic Opening Vents (AOV’s) or Smoke and Heat Exhaust Ventilators (SHEV’s), in the roof or façade.
This approach relies on the buoyancy or stack effect of the smoke laden warm air; Ensuring that the overall system will operate correctly requires a well-designed and delivered combination of components that make up the overall smoke system, to ensure the smoke is adequately ventilated under various environmental and operating conditions.
The system components may include AOV’s, Roof Vents, Smoke Dampers, Smoke Shafts, Atrium Vents, Make Up Air Vents and may be supplemented by or work alongside elements of mechanical ventilation like fans. Smoke detectors and break glass units are normally attached to the smoke control system panels to trigger demand for smoke ventilation at the detected fire location.
The way the system and vents should operate is usually described through the DesOps (description of operation) or Cause and Effect – setting out which vents should open and which vents should close according to the initial detected fire location.
Recent changes to BS9991 in 2024 instruct that the use of Natural Smoke Ventilation be limited to buildings up to 30m in height providing maximum travel distance is no more than 7.5m (15m with a sprinkler system installed), beyond which mechanical smoke ventilation is required.
What is Mechanical Smoke Ventilation?
Mechanical smoke ventilation systems use fans and a combination of components to create pressure differences that either extract smoke from key areas of the building (in the case of a mechanical smoke extraction system) or prevent smoke entering them (in a stair pressurisation or pressure differential system).
They both most commonly using roof mounted fans in conjunction with ‘smoke shafts’ or ductwork via dampers opened to the floor where smoke is first detected. Depending on the strategy, they use the fans to either pull air out of the space using strategically positioned automated opening vents providing makeup air, or they intentionally pressurise the protected space to make it more difficult for smoke to enter it from the fire location.
Mechanical smoke ventilation is most often employed in larger, very tall or complex buildings and where natural smoke ventilation systems may be impractical, inadequate or require mechanical support. They may however include some element or components commonly used in natural smoke ventilation systems.
There are pros and cons of each depending on the application and budget, but these include things like cost, space, secondary power supplies and battery backup, complexity, maintenance etc. Whichever approach is selected, it must be fit for purpose, however there are some general observations on the benefits of each.
The benefits of Natural Smoke Ventilation
Natural smoke ventilation relatively simple to design and implement using a standard approach where the building design meets the prescribed requirements of approved document B and where BS9991 allows.
Natural smoke ventilation typically costs less and integrates better into the aesthetic of the building using discrete components like AOV windows, AOV louvres, AOV dampers and AOV rooflights.
AOVs for natural smoke ventilation normally use extra low voltage (24v DC) components which means they normally only require battery backup as a secondary power supply to continue to operate the system in the event of mains power failure or fire affecting primary mains power supplies. With detectors, panels and vents being designed to run off 24v DC, this means that battery backup is more cost effective than backup mains power or UPSs required for ongoing operation of mains powered fans which must continue to run in mechanical ventilation solutions.
What’s more, fans can be noisier when operating, and once natural smoke vents are fully opened, they are normally designed to maintain their opening position and free area even when power is no longer available, whereas mechanical smoke ventilation requires ongoing power to run fans.
Natural ventilation may be less preferred because:
- May be more difficult to implement in large complex buildings or where design could be affected by adverse weather conditions.
- Cannot be used in buildings over 30m tall.
- If floor area is a premium, natural smoke ventilation shafts can take up a small amount of additional floor area as they may need to have a bigger cross-sectional area (1.5m2) and larger associated dampers compared with mechanical ones that utilise smaller section sizes and specific fan powers to ensure sufficient flow rates.
The benefits of Mechanical Smoke Ventilation
Mechanical smoke ventilation is prescribed for taller buildings over 30m and where the building is large or complex, requiring the flexibility to be able to ramp up and ensure sufficient air flow rates or pressures are achieved.
Where floor area is a premium, mechanical smoke ventilation can reduce the amount of floor area taken up by the system, releasing it for other purposes.
Mechanical systems may be less preferred because:
- They require a secondary mains power supply to continue to operate fans for as long as required (batteries aren’t normally a viable option)
- Higher capital cost and potential more complex testing and maintenance costs
Choosing the right smoke ventilation system
Which systems or approaches are employed, or the combinations of both, will be determined by the design teams, with Architects, Consultant Engineers and specialist Fire Engineers contributing input to the analysis, drawings and specifications that normally set out the requirements of the buildings smoke ventilation systems.
Fire and life safety is now a sufficiently important topic for building designers that it is mandated within the CPD learning requirements by the Architects Registration Board (ARB) in the UK
https://arb.org.uk/architect-information/cpd/mandatory-topic-guidance/
The components that make up the final system design and installation must be selected to achieve the required operational capabilities and performance set out in the design and must meet all the relevant product standards and legislation.
As well as design of the system and performance of the components, installation and proving of the system is also covered by regulations, as is the requirement for ongoing testing and maintenance to ensure the systems will always operate as expected should they need to.
All these elements must be overseen by competent individuals or organisations according to their role and in line with the relevant regulations.
What are the regulations for smoke ventilation?
As smoke ventilation systems serve a critical life safety function within buildings, the design, products, installation, testing and maintenance of the systems are covered by an array of laws, building regulations and products standards – incorporating EN (European Norm), ISO and British Standards which must be complied with.
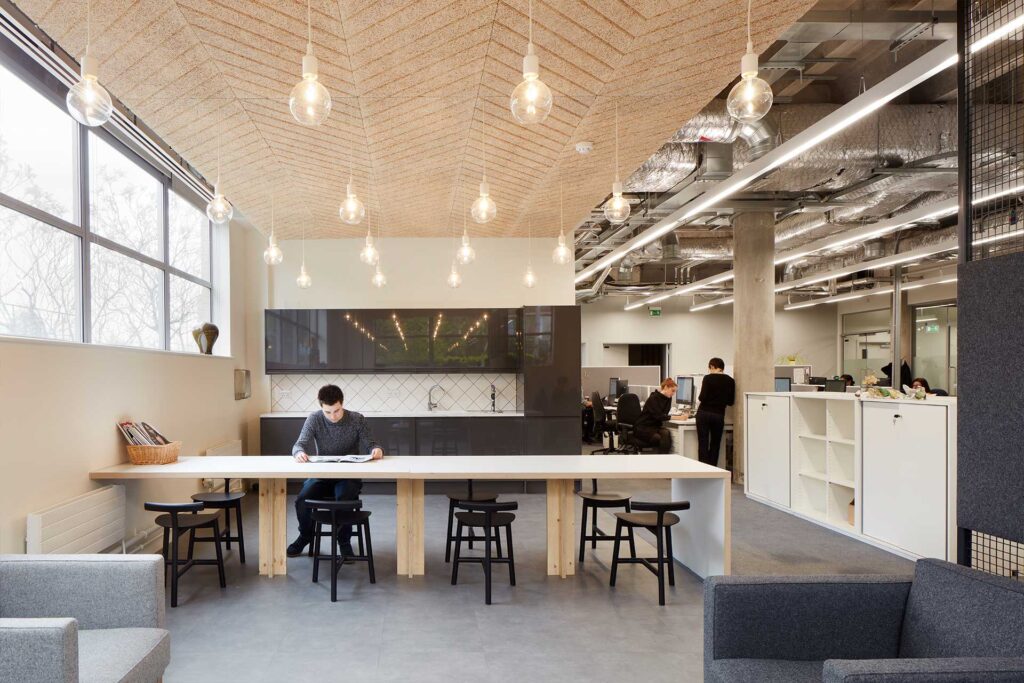
Smoke ventilation and the regulations – a brief overview.
Introduction to smoke vent standards and regulations:
Smoke Ventilation systems play a critical role for the safety of building occupants in larger and multi storey buildings, where they are called upon in the event of a fire to keep escape routes clear of smoke and help ensure occupants are able to safely exit the building.
Commonly employed in high rise residential, commercial, education, hotel and industrial buildings – smoke ventilation systems are subject to a variety of standards and regulations to ensure that the smoke ventilation strategies and components that deliver them will operate correctly and can be depended upon in the event of a fire.
The suite of regulations and standards offer guidance and impose legal requirements for the various parties involved with the design, installation, and maintenance of buildings. They help understand responsibilities and outline the means of fulfilling them, ultimately to ensure the ongoing safety of occupants throughout the life of the building.
All parties involved with the associated design and specification, product manufacture, purchasing, installation, management, and ownership of buildings with smoke ventilation systems, should therefore ensure they are familiar with the latest standards and regulations, and be confident and able to demonstrate their compliance to fulfil their legal duties and keep occupants safe.
Here’s our guide:
This guide introduces the various regulations which can be used to help develop effective, compliant designs and ensure conformant product selections. They also help govern that installations are adequately delivered and properly documented, and that post occupancy testing, and service is maintained and recorded according to regulatory requirements.
UK Regulatory Framework:
The main government led legal standards are set out and enforced via –
- The Building Regulations and Approved Documents
- British Standards (incorporating EN and ISO standards)
- Construction product regulations (and CE / UKCA marking)
- Fire Safety Regulations and Regulatory Reform Order Laws
Smoke Ventilation and The UK Building Regulations
Navigating the various standards regarding Smoke Ventilation normally begins with The Building Regulations in England and Wales, starting with Approved Document B – Fire Safety, also commonly referred to as “ADB”. This specifically sets out the requirements for smoke control systems in new and existing buildings.
What is approved document B?
Approved document B is part of the UK building regulations and provides guidance on fire safety in and around buildings, including topics such as means of escape, fire spread, protection, and access for fire services. It outlines when and how fire detection, protection, and smoke ventilation measures must be employed.
Approved Document B – Fire Safety:
Like most other sections of the buildings regulations, two volumes for ADB exist; Volume 1 applies to Dwellings (now including blocks of flats previously represented in vol 2 prior to 2019), and Volume 2 for buildings other than dwellings. Compliance with these for fire safety is a mandated requirement for building designers, builders and owners.
ADB also refers to a whole suite of other British, EN and ISO standards that we will refer to later.
While Part B is the main document from the building regulations referenced for fire safety, other parts of the building regulations may also be relevant to the design and product selections, for example;
Approved Document F (Ventilation):
ADF offers information into approaches for acceptable building ventilation, considering factors such as air quality, humidity, condensation, and fumes. The main crossover with smoke ventilations systems is where there is an intention to use smoke ventilators as part of other day to day and environmental ventilation requirements for the building (noting that the components used must be suitable and rated for dual purpose, and compliant with the standards that govern such products).
Approved Document L (Conservation of Fuel and Power):
ADL provides information on enhancing building energy efficiency, with a focus on minimizing heat loss, improving insulation (including U values for windows and smoke vents), air permeability testing, boiler efficiency, and lighting standards. It also offers performance factors and standards for heating, ventilation, and control systems. The main relevance regarding smoke ventilation is the requirement for smoke vents to maintain compliance in terms of preventing excessive heat loss, and that U value requirements are met; U-Values are the unit for measuring heat loss and the lower the U-Value, the smaller amount of heat transmittance or heat loss. To comply with Approved Document L, any windows must meet the relevant U Value requirements, and roof ventilators (including smoke vents) must have a U-Value of 3.0 W/m2k or lower.
What are the regulations in Scotland for smoke ventilation systems?
The Building (Scotland) Regulations 2004 state ‘Every building must be designed and constructed in a way that in the event of fire within the building, the occupants, once alerted to the outbreak of fire, are provided with the opportunity to escape the building, before being affected by fire or smoke’.
The Building (Scotland) Regulations 2004 are supported by the Building Standards Technical Handbooks
Building Standards Technical Handbook: Domestic and Non-Domestic
The building standards technical handbooks provide guidance on achieving the Building (Scotland) Regulations. The documents mandate that everyone within a building should be provided with at least one means of escape from fire, offering a safe passage and allowing them to escape from the building before being affected by fire or smoke.
Scotland: In Scotland the Building Standards Technical Handbook states that every corridor that may be utilised as an escape route and that exceeds certain dimensions should be subdivided by a fire resistant wall, or protected by the installation of a smoke control system.
The domestic guide describes fire protection measures including active systems such as automatic detection, automatic smoke ventilation and automatic suppression to provide early warning, control heat and smoke and inhibit fire growth. All escape strategies use a combination of passive and active fire protection measures. It defines the need for automatic smoke ventilation to be provided within every protected lobby serving a single escape stair in a domestic building and that smoke ventilation may be provided by natural smoke ventilation, or mechanical smoke ventilation.
They also outline information about natural ventilation openings and smoke shafts, and the required free areas with further reference to EN12101.
What about smoke ventilation and the regulations in Wales and Northern Ireland?
Wales also has its own version of Approved Document B although currently they are very similar for the purposes of this document. Northern Ireland also has its own technical booklet E. The guidance of all these documents are similar, but parties serving specific regions should refer to their local standards and legislation to ensure they are met. The remainder of this document will focus on the standards in England for simplicity.
What are the regulations, standards and design guides for designing smoke ventilation solutions?
BS9991:2024 Fire safety in the design, management and use of residential buildings. Code of practice
BS9999: Code of practice for fire safety in the design, management and use of buildings
BS7346-8: Code of Practice for planning, design, installation, commissioning and maintenance of smoke control systems
BS7974: Application of fire safety engineering principles to the design of buildings
The various standards call upon design teams to have carried out a fire risk assessment to ensure the end solution will be fit for purpose according to factors like building size, type, occupancy profile, contributory fire risks, compartmentation and exit routes.
Best practice approach to smoke ventilation design
Approved Document B of the English Building Regulations offers specific guidance on fire safety and smoke control measures for different types of buildings, as well as prescribed approaches for different applications. Designers and builders must ensure compliance with these regulations.
Designers will typically either follow ADB guidance which sets out typical approaches for common building situations, or consider ‘fire engineered solutions’ which must demonstrate that the building achieves at least as good performance as ADB and meets the requirements of the building regulations. BS7974 is referenced by ADB as a framework for fire safety engineered solutions during design.
ADB offers guidance on possible solutions for buildings according to prescribed limits of things like building arrangement, height, dimensions and distances to stairs and escape routes.
By way of example, ADB vol 1. Section 3 considers means of escape in flats and offers a simplified and standardized approach to smoke vent solutions to protect common escape routes. One of which is the possibility of Natural Smoke ventilation using typical vent sizes in agreed locations (providing that all other elements of the building meet requirements of the prescribed approach);
Excerpt from ADB (2019 edition incorporating 2020 and 2022 amendments):
Smoke control in common escape routes
3.49 Despite the provisions described, it is probable that some smoke will get into the common corridor or lobby from a fire in a flat.
There should therefore be some means of ventilating the common corridors/lobbies to control smoke and so protect the common stairs. This means of ventilation offers additional protection to that provided by the fire doors to the stair, as well as some protection to the corridors/lobbies.
Ventilation can be natural (paragraphs 3.50 to 3.53) or mechanical (paragraph 3.54).
Smoke control of common escape routes by natural smoke ventilation
3.50 Except in buildings that comply with Diagram 3.9 (small single stair building), the corridor or lobby next to each stair should have a smoke vent. The location of the vent should comply with both of the following.
a) Be as high as practicable.
b) Be positioned so the top edge is at least as high as the top of the door to the stair.
3.51 Smoke vents should comply with one of the following.
a) They should be located on an external wall with minimum free area of 1.5m2 or
b) They should discharge into a vertical smoke shaft, closed at the base, that meets all of the following criteria.
i) The shaft should conform to the following conditions.
-
- Have a minimum cross-sectional area of 1.5m2 (minimum dimension 0.85m in any direction).
- Open at roof level, minimum 0.5m above any surrounding structures within 2m of it horizontally.
- Extend a minimum of 2.5m above the ceiling of the highest storey served by the shaft
ii) The free area of all the following vents should be a minimum of 1m2 in the following places.
-
- From the corridor or lobby into the shaft.
- At the opening at the head of the shaft.
- At all internal locations within the shaft (e.g. safety grilles).
iii) The smoke shaft should be constructed from a class A1 material. All vents should either be a smoke leakage (Sa) rated fire doorset (see Appendix C, Table C1, item 2.e for minimum fire resistance) or fitted with a smoke control damper achieving the same period of fire resistance and designed to operate as described below. The shaft should be vertical from base to head, with a maximum of 4m at a maximum inclined angle of 30 degrees.
iv) If smoke is detected in the common corridor or lobby, both of the following should occur.
3.52 A vent to the outside with a minimum free area of 1m2 should be provided from the top storey of the stair.
3.53 In single stair buildings, smoke vents on the storey where the fire is initiated, and the vent at the head of the stair, should be activated by smoke detectors in the common parts.
In buildings with more than one stair, smoke vents may be activated manually. The control system should open the vent at the head of the stair before, or at the same time as, the vent on the storey where the fire is located. Smoke detection is not required for ventilation purposes in this instance.
Smoke control of common escape routes by mechanical ventilation 3.54
Guidance on the design of smoke control systems that use pressure differentials is available in BS EN 12101-6.
Note. In November 2020 Approved Document B was also updated to reduce the threshold for installing sprinkler system in residential and mixed use buildings where they have at least one floor above 11m from outside floor level.
If the design deviates from the common models offered in ADB, it will need to be a fire engineered solution where qualified fire engineers simulate and assess the risks and impact from fire, and engineer a solution specific to the building capacity, use, and layout.
BS7974 (amongst the other standards) is a common point of reference when developing these solutions.
What is the required free area of a smoke vent or automated opening vent (AOV)?
Approved Document B sets out typical prescribed free areas for smoke vents of 1m2 or 1.5m2 depending on their location. It allows an aerodynamic or geometric measurement of the free area and offers guidance on how it may be calculated. Fire engineered solutions may require different areas.
The common free areas of smoke vents as set out in Approved Document B are as follows:
For small single stair buildings as defined in ADB, using Natural Smoke Ventilation require vents for the fire and rescue service and should be either a:
High level openable vent at each storey OR | 1m2 minimum free area |
A single openable vent at the head of the stair operable remotely at the fire and rescue access level | 1m2 minimum free area |
Section 3.28 states
For buildings other than small single stair buildings utilising Natural Smoke Ventilation:
Vents to external walls serving the corridor or lobby next to each stair | 1.5m2 free area vent located as high as possible and with the top edge at least as high as the top of the door to the stair.
|
Vents into natural ventilation smoke shafts | 1m2 free area from the corridor or lobby into the shaft, and 1m2 free area for the vent at the head of the shaft |
The ‘free area’ as defined by Approved Document B, can be measured and taken as either:
- The declared aerodynamic free area in accordance with BS EN 12101-2.
- The total unobstructed cross-sectional area (geometric free area), measured in the plane where the area is at a minimum and at right angles to the direction of air flow (Diagram D7).
How do you calculate the free area of a smoke vent or AOV?
Approved Document B allows the free area of a smoke vent to be calculated either by using a geometric free area measurement based on the unobstructed opening area at 90o to the smoke flow, or test-based calculations of aerodynamic free area as required for BS EN12101-2 declarations of performance.
ADB offers guidance on the method of calculating free area to satisfy the 1 and 1.5m2 geometric free area requirements in the standard, as follows:
Calculation tools like that from WindowMaster can help give a useful estimate of the geometric free area of a window, however more precise calculations and measurements are required specific to the final vent arrangement to calculate the actual geometric free area. https://www.windowmaster.com/resources/calculators/actuator-finder
Geometric free area is not the same as the aerodynamic free area that must be tested and proved by the manufacturer of the AOV and stated as part of the declaration of performance (DoP) of the complete AOV before it is put on the market.
Additional guidance from the Smoke Control Association
The Smoke Control Association offers further guidance on how to interpret and apply the various smoke ventilation standards and clarifies the calculation methods as applicable to geometric free areas defined in ADB and the requirements of EN12101-1.
The SCA produces a useful range of resources. including downloads and member services to those parties involved with design, installation, and servicing of smoke ventilation systems, which can be found here https://www.smokecontrol.org.uk/resources
The SCA guidance contains the following free areas methodology guidance notes:
In summary, the guidance from the Smoke Control Association states a preference to use the Aerodynamic Free Area as declared in BS EN12101-2 certification and declaration of performance (DoP) from the AOV manufacturer, rather than a geometric calculation wherever possible.
The Smoke Control Association guidance may be useful and provide best practice guidance for consideration in parallel to regulations – noting that it would not normally supersede official guidance until such time as their recommendations are mandated as part of updates to standards.
What are the British standards for smoke ventilation?
Several British Standards are referenced by the approved documents of the Building Regulations, and these provide further guidance on the design, installation and maintenance of the smoke ventilation systems, including requirements for the products that make up those systems. These include BS7346, BS9991, BS9999 & BS7974 more info here.
BS7346-8: Code of Practice for planning, design, installation, commissioning and maintenance of smoke control systems
BS 7346 draws upon and consolidates a broad range of regulations and guides and provides a good overview and a unified code of practice and guidance through all stages of smoke control system design, installation and ongoing testing and maintenance.
The guidance considers product quality requirements, practical positioning, performance and operation, as well assessment and certification. The standard is provided to make the end to end process of designing, installing and maintaining compliant smoke control systems easier to understand and refers to the other relevant standards for more detail.
It provides a good starting point and reference document for anyone trying to understand more about smoke standards.
BS9991:2024 Fire safety in the design, management and use of residential buildings. Code of practice
BS9991 focuses on residential buildings and sets out that risk assessments, suitable fire safety measures and procedures must be established during design of residential buildings.
It gives recommendations and guidance on the design, management and use of residential buildings so they achieve reasonable standards of fire safety for people who are in and around them, and that associated ongoing testing and maintenance is fulfilled by the responsible party using trained and competent persons.
What are the recent changes to BS9991 in 2024 for smoke ventilation?
The new BS9991:2024 edition updates guidance for Smoke Ventilation Systems including 18m building height limits for the use of corridor AOVs directly to outside, a maximum building height of 30m for natural smoke ventilation, & pressurisation systems for buildings over 60m, as well as daily fault checks on smoke panels
In addition, it states that buildings over 11m should now have suitable sprinkler systems, buildings over 18m must have evacuation alert systems to BS8629 to allow fire officers to alert occupants of evacuation instructions as well as a recommendation for more than one stairwell. Much taller buildings should also have evacuation lifts which can also serve as dual purpose fire fighting lifts for buildings over 50m.
BS9999: Code of practice for fire safety in the design, management and use of buildings
BS9999 sets out design guidance, and further requirements for routine maintenance, inspection and testing of smoke ventilation systems.
It gives particular attention to the need for fire safety equipment to be regularly inspected by competent persons, and recommends that servicing is overseen by a specialist organisation in line with the relevant standards. It suggests that Smoke ventilation systems should be tested weekly along with a functional test of all system components.
BS7974: Application of fire safety engineering principles to the design of buildings
BS 7974 provides guidance for the application of fire safety engineering (FSE) principles to the design of buildings.
It offers guidance and recommendations for the safety and protection of people, property and local environment from the risks of fire and is supported by the PD 7974 series of documents setting out how to tackle analysis of building fire safety requirements. This set of documents is most relevant to fire safety engineers as part of the risk assessment and design of the building.
Compliance with these standards should be evidenced through documentation and proper record keeping throughout the design, delivery and ongoing building maintenance to demonstrate adherence with best practices and regulatory guidance.
What are the product standards for components of Smoke Ventilation Systems?
The main standards applying to products used in smoke ventilation systems are covered in the construction product regulations and the BS EN12101 suite of standards – requiring adequate testing, manufacturing control, record keeping and performance declarations from the product manufacturers to ensure product performance and reliability can be depended upon.
In addition to the regulations and standards relating to services and servicing of smoke ventilation systems, specific product standards exist regarding the testing, proving and certified performance and reliability of products applied in life safety smoke ventilation systems.
The Construction Product Regulations and Product standards
In 2013 the Construction Product Regulations mandated that all construction products covered by a harmonised European Norm (hEN) must be CE marked to demonstrate compliance with the relevant standards. For Smoke Ventilation systems the relevant suite of standards is EN12101 – since adopted into the British standards as BS EN 12101, and significantly mirrored in emerging ISO 21927 standards for non European Communities.
BS EN12101 and CE / UKCA Marking
EN12101 comprises a suite of standards that define necessary testing and performance requirements for individual smoke ventilation system components, such as fans, control panels, smoke vents, and dampers.
All components must be designed, tested, built and documented by the manufacturer in accordance with the relevant EN12101 performance and quality standards.
In order to clearly demonstrate compliance, the products put on the market must bear a CE or UKCA mark and be accompanied by a declaration of performance (DoP).
The DoP normally appears in the form of an attached label showing manufacturer, product and performance information, and a certificate bearing the items tested and declared performance capabilities. This marking and documentation is part of the thread detailing the component manufacturer’s information and its commitment to its product performance.
There is currently a transition underway from CE marking to UKCA marking, and what will be allowable in the future is currently under review and subject to ongoing guidance. Currently in 2024 either CE or UKCA marking is acceptable however guidance is subject to change with further reviews and advice to follow for key dates in 2025 and 2028 regarding acceptable means of achieving certification and labelling.
Here’s an example from the WindowMaster guide to EN12101 and FPC requirements of what a typical CE mark and Declaration of performance might look like, although manufacturers are responsible for the format and which essential characteristics or performance declarations are required for their product.
EN 12101, Smoke and heat control systems, consists of the following parts:
- Part 1: Specification for smoke barriers ― Requirements and test methods
- Part 2: Specification for natural smoke and heat control ventilators
- Part 3: Specification for powered smoke and heat control ventilators
- Part 4: Natural smoke and heat control ventilation systems – Installation and test methods (published as CEN/TR 12101-4)
- Part 5: Design and calculation for smoke and exhaust ventilation systems (published as CEN/TR 12101-5)
- Part 6: Specification for pressure differential systems- kits
- Part 7: Smoke duct sections
- Part 8: Smoke control dampers
- Part 9: Functionality of smoke control panels (Note: this is a proposed draft and not yet mandated)
- Part 10: Power supplies
- Part 11: Smoke control in car parks
- Part 12: SHEVS – Time dependent fires
- Part 13: Pressure differential systems (PDS) design and calculation methods, acceptance testing, maintenance and routine testing of installation
Fire Safety Laws and Regulations
The Fire Safety Act 2021
The Fire Safety Act 2021 was introduced to clarify the scope of fire risk assessments required under the Regulatory Reform (Fire Safety) Order 2005 and applies to non-domestic buildings and common areas of high rise residential buildings. The act calls for more regular and extensive assessments and record keeping, and that interim assessments must take place at change of ownership or building manager in order to maintain the seamless protection of occupants.
Fire Safety (England) Regulations 2022
In June 2022, the Fire Safety (England) Regulations 2022 were introduced adding further detail and requirements particularly with regard to persons responsible for high rise buildings. This clarified a need for lodging and maintaining up to date floor plans, fire strategies and equipment information with local fire and rescue services, as well as making information available to residents and maintaining it in a secure location in their building along with floorplans and contact details of the responsible person.
The responsible person is also required to oversee logs of regular checks and report defects and remedial measures as part of ongoing testing and maintenance responsibilities.
Installation of smoke ventilation systems and components
Throughout the various standards and regulations, it is clear that installation and maintenance of smoke ventilation systems must be carried out by competent persons and organisations.
Demonstrating competence is often achieved through accreditation with recognised industry bodies like BAFE (British Approvals for Fire Equipment) and the Smoke Control Association via its SDI 19 Smoke Control installation and accreditation scheme in partnership with the UK notified body IFC Certification.
Commissioning, Testing and sign off:
An important part of the installation, final commissioning and sign off of the system before handover involves rigorous testing of the system to verify performance and compliance. This may include simulated smoke extraction testing, airflow measurements and extensive operational checks.
Here’s a summary checklist of some of the key elements for new building handover (please refer to the relevant standards for more information);
- O&M Manual for the system, along with cause and effect and design specifications in place
- Product testing, certification and DoP records in place
- Who are the designers responsible for the system solution and design. Is there evidence that the solution has been designed appropriately; is there a designer risk assessment and or fire engineers report that reflects the building and system as installed.
- Who was responsible for selecting the various components and who was responsible for installing each/all elements of the smoke ventilation system. Have the installers of all components provided evidence of their competency and accreditation to install and commission the system. Are contact details provided and up to date.
- Have all suppliers provided full records of the equipment purchased.
- Have the installers provided full records of the equipment installed along with commissioning and testing certificates.
- Have building plans, system information and fire strategy been lodged with local fire and rescue services along with responsible person contact details.
- Has a competent person/company been appointed to oversee the required testing and maintenance of the system. Has record keeping for same been agreed.
- Has all documentation been stored securely (and digitally) in a declared location and relevant information about the systems and strategies in place been made available to building occupants.
- Have ‘high risk’ (over 7 storey or 18m) buildings been registered with the Building Safety Register prior to occupancy, and rules of the golden thread been followed.
- Is the responsible person aware of their responsibilities to maintain building records, up to date fire risk assessments, and remain informed of latest guidance and standards.
Testing and Maintenance of Smoke Ventilation Systems
Regular testing, preventative maintenance and emergency repair are essential to maintain the reliable operation of the system in the event of a fire, and to demonstrate ongoing legal compliance. Building owners and managers are therefore incumbent to adhere to prescribed testing, inspection and maintenance requirements, and properly document them through testing and inspection schedules, risk assessments and maintenance activities.
The Regulatory Reform (Fire Safety) Order 2005 consolidates previous legislation and clearly sets out responsibilities for fire safety solutions:
‘Building owners and managers are responsible for adequate fire safety solutions in their buildings. As the responsible person, they must ensure systems and components are adequately tested, and maintained to function as expected in the event of a fire. They must also ensure that any company providing servicing is adequately qualified to do so.’
In 2022 the Fire Safety (England) Regulations 2022 were introduced alongside the Building Safety Act (2022). These emphasize and add to the requirements of the Regulatory Reform (Fire Safety) Order 2005 with more comprehensive demands on building owners and managers to continuously assess and maintain records of the risks of fire in high rise buildings, and the systems and measures in place to negate them. Occupants should also be given key information about the systems, fire strategies, and ongoing activities that protect them. Since these new acts were introduced, building owners must advise local fire and rescue services with any faults relating to the system that cannot be rectified within 24 hours.
How often should a smoke ventilation system be tested?
EN12101, BS9999:2017 Annex I and BS7346-8 set out the frequency of tests required for smoke ventilation systems. These require weekly function tests, more comprehensive monthly system tests, and extensive system and component testing and maintenance by a competent engineer at least once per year.
Smoke Ventilation System testing should be in accordance with BS9999 guidelines and functional tests often form a part of the planned weekly fire alarms tests.
Weekly function tests normally consist of manually triggering the system and ensuring all components operate as expected and trigger the expected response from the system.
More comprehensive monthly tests may involve primary power supply failure being simulated to test backup power devices and batteries, depending on the system and O&M recommendations alongside regulatory guidance.
Records should be kept of who (with appropriate knowledge of the system) conducted the tests, when, and comprehensive records of the testing procedure and outcomes, along with any additional remediation requirements and notifications being instructed.
BS 7346-8 states that more extensive testing and maintenance must take place at least once per year by ‘competent’ engineers or smoke vent specialists who normally follow a twice a year inspection and record keeping regime. The annual or biannual inspections should include testing all components and cross referencing the system cause and effect – verifying that reliability and performance requirements continue to be met and identifying any potential maintenance that may be needed in the short or long term.
Batteries should normally be replaced every 4 years or on a failed performance or capacity test whichever is sooner.
If any testing or maintenance highlights potential shortfalls in terms of system performance or risk, it is the building owner or delegated managers responsibility to make sure a risk assessment is conducted, and urgent and appropriate remedial action taken – which may include consulting local fire and rescue services, and residents as appropriate.
Industry experts like www.tealproducts.com have extensive partner networks of competent installers and service technicians, and often carry emergency spares available for next day delivery.
What is a competent person for maintaining smoke ventilation systems?
While the definition of ‘competent’ person is not clearly defined in regulations, it is the building owner or managers responsibility to ensure that any third party or individual conducting testing and maintenance demonstrates sufficient specialist knowledge, training and experience to do so in line with regulations and uphold building safety.
They must also have properly documented their compliance in achieving that, and a plan to maintain that for as long as they are responsible for the works. The easiest and most comprehensive way of achieving that is often to provide details of accreditation to schemes like SDI 19 or other industry associations that require ongoing training and record keeping by member organisations to demonstrate competence and compliance.
What about replacement parts and actuators to AOVs?
It is generally deemed that maintenance of any component of a smoke ventilation system must have been conducted by a competent person, and that any works to or replacement parts of those components must as a minimum demonstrate that it maintains its certification and performs as well as or better than when it was installed, as well as being fit for purpose. Routine risk assessment and maintenance may highlight a need to upgrade or replace systems in existing buildings to bring them up to and in line with the latest performance standards and regulations.
A Final Word on Documentation and the Golden Thread
Documenting what has been delivered, by who, their competencies, certification around products used, and evidence of testing and performance in situ, as well as ongoing maintenance records is key to ensuring confidence in the systems suitability, performance and ability to do its duties at any time should it be called upon.
What is the Golden Thread?
The Golden Thread concept was introduced in the UK’s building safety bill following the Grenfell fire tragedy. It sets out requirements for the systematic management of building information through its life cycle, ensuring critical information about a building’s design, construction and maintenance is properly documented, and accessible to relevant parties.
The Golden Thread aims to embed and secure accountability and transparency in building documentation – and ultimately improve safety of buildings through clear and traceable records of responsibility – from design through build, occupancy, testing and maintenance.
It applies particularly to higher-risk and high-rise residential buildings which have at least 7 storeys (or are at least 18 metres high), with 2 or more residential units (or which are a care home or hospital). These buildings must be registered with the Building Safety Regulator before being occupied (or by Apr 23 for existing buildings), and meet the requirements for securely and digitally storing a buildings documentation and ‘single source of truth’, making all records available to relevant parties should they be required.
Designers, building owners, and contractors of high risk buildings should follow the extensive requirements for the meeting the requirements of the golden thread as set out in The Building (Higher-Risk Building Procedures) (England) Regulations 2023
Evolving standards and guidance
This guide offers an introduction to a complex suite of standards and is believed to give an accurate overview at the time of production in April 2024, however, guidance is in some respects open to interpretation and ever evolving. It is the readers responsibility to familiarise with all relevant standards and draw their own conclusions or seek specific advice on their application and obligations to ensure they are compliant.
Other interim guidance, best practices and supplementary notes also exist from parties like the Smoke Control Association (SCA) and Fire Officers Association – often being reviewed and incorporated in future revisions to standards and building regulations.
In summary, smoke ventilation regulations and certification underpin the safe and proper design, installation and maintenance of smoke ventilation systems. Designers, builders, building owners and managers must adhere to these regulations to ensure the effective implementation and ongoing operation of these life critical systems to continue to safeguard occupants in the event of a fire and throughout the life of the building.
This article was produced for Teal Products in collaboration with Northern Shoal Consulting
Glossary
Useful resources:
Local Authority Building Control – LABC Guide to fire engineered solutions – https://www.labc.co.uk/sites/default/files/labcpd0914_techg_fireengineered.pdf
WindowMaster guide to EN12101 and CE marking:
https://www.windowmaster.com/media/osdkbscs/fpc-smoke-guide-eng-v2.pdf
- Want help with smoke ventilation design or finding the right products?
- Want product supply or system installation for your next smoke project?
- Want training on smoke ventilation or to become a teal products partner?
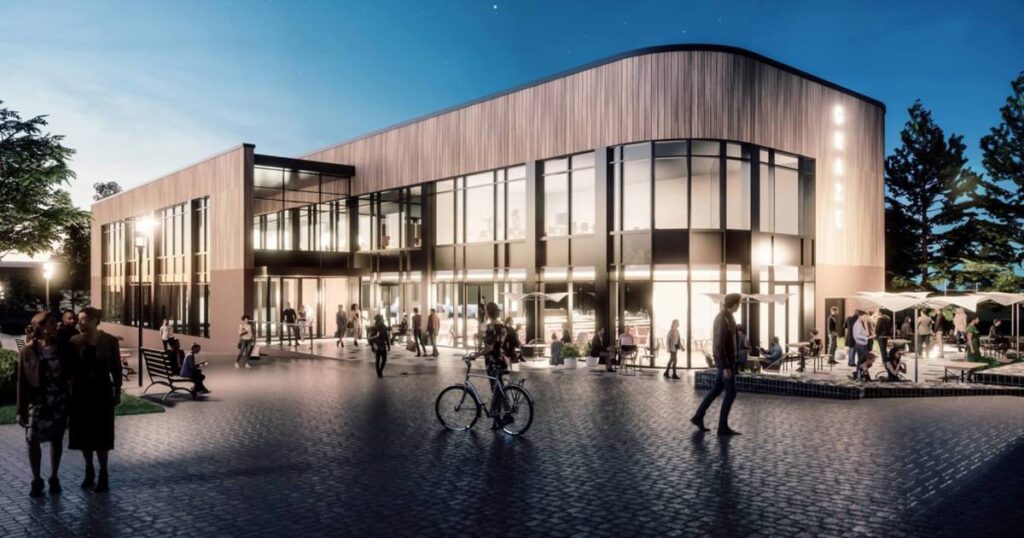
About Teal Products
Teal products are an expert distributor and SDI 19 approved installer of a broad range of smoke ventilation solutions and products from a wide range of manufacturers. With over 20 years of experience, and a wide range of stocked products at our HQ in Gloucestershire serving the whole of the UK– we offer design guidance, product advice and help with regard to standards or finding competent providers of services through our partner network. Follow us on LinkedIn for more industry news and useful articles: https://www.linkedin.com/company/teal-products-ltd/ For more examples of smoke ventilation system components supplied by Teal Products visit us here: https://tealproducts.com/resource/smoke-control-equipment Contact us by telephone 01242 620 318 or send an email to sales@tealproducts.co.uk
Contact Us